These wonderful 3 dimensional copper stamps, called tjaps or chops, have been used for quite a number of decades now in Indonesia for applying wax in the art of batik, and are collected as pieces of art in their own right by collectors, also by artisans in other countries to use. For awhile, the modern miracle of being able to print fabrics with traditional batik designs caused a lot of batik factories to close in Indonesia, as true batik is, by comparison, unbelievably labor intensive. But caches of the intricate copper chops that had been used all over the country still remained. Some of them have been "discovered" and now you can find them for sale occasionally. You can also go to Indonesia where artisans still exist who know how to make them, but these days having a new one made to order will cost you in the neighborhood of $200-300.
True batik is now enjoying resurgence in popularity, so more batik businesses in Indonesia are re-opening or starting up, and putting the tjaps that remain in the country back into use. Hence they are becoming scarce for collectors or artists outside the country. Dharma Trading Co. has been fortunate to have a contact over there that can still source some pretty nice old tjaps at comparatively reasonable prices.
History-
Applying wax with a Tjanting (also called canting) takes a lot of skill and is very time-consuming. One sarong can take up to 3 months to make when drawing all the intricate design work in traditional Indonesian batik by hand. For hundreds of years, only royalty could afford it. As the commercial demand for batik rose, time saving methods evolved to allow for faster production of these designs. Other methods of applying the wax to the fabric included pouring the liquid wax, painting the wax with brushes, and putting hot wax onto pre-formed copper stamps or tjaps and stamping it onto the fabric. Copper is used because of it's excellent heat conducting properties, so it keeps the wax liquid the longest.
The copper tjap was developed by the Javanese in the 20th century and it revolutionized batik production. By block printing the wax onto the fabric, it became possible to mass-produce designs and intricate repeating patterns far faster than one could possibly do by using a canting.
How Tjaps are made-
A Tjap is basically a stamp, but flat-faced stamps do not hold hot wax well enough to really print with. It has to conduct heat, and be three dimensional so the wax can be held on a larger surface but print a delicate design. Tjaps are made with narrow strips of copper that are twisted and shaped into batik designs, then soldered to less conductive open steel base with a handle. They are made based on designs drawn out by the batik artist just on a piece of paper. For the skilled copper craftsman, a simple sketch is all they need.
Traditional & Modern Use-
In traditional batik, tjaps are just used to apply wax to fabrics. Melted wax for stamping is kept in a flat-bottomed pan, traditionally called a layang, with piece of folded cloth laid in it that absorbs the wax and acts like a stamp pad. The tjap is dipped into the hot wax, then applied to the cloth which is stretched out on a padded table that absorbs the pressure of the stamp. Once the fabric is completely printed and the wax is cool it is vat dyed and the wax is boiled out.
You can check out how to use your tjap with wax here
As used tjaps have become popular in the US and other countries modern textile artists are using them in new ways. Instead of just using them to apply wax, artists are using other types of resists, all natural non-wax resists that can achieve a batik like look but that do not have the same issues with heating and possible toxic fumes that wax does; check it out. They also work will with Soy Wax, which doesn't give off fumes, and cleans up with soap and water.
Tjaps are also used for stamping thick printing inks and also glues; using foil glue (#IDFG) artists can stamp these beautiful patterns that then dry tacky and metal foils like the iCraft Deco Foil (#IDF6) can be rubbed on for beautiful effect and intricate patterns. This makes a wonderful embellishment on hand dyed fabrics.
Aside from using them to print on fabrics they have also become popular among collectors as objects d'art just in and of themselves.
Care and Cleaning-
In order to keep your Tjap in working condition for years to come, it is important to clean them immediately after use. You should also avoid using discharge pastes because they will react with the copper. If you want to discharge the design on your Tjap it is better to make a stamp or silk screen of the design by scanning the face of the tjap - you can check out our tutorial on how here
After use with any water based product, including Soy Wax, it is best to clean them at the sink under warm to hot running water with a brush with somewhat softer bristles, gently, so as not to damage any of the delicate copper design work. Then if it is a nice warm day, put them out in the sun to dry. In the winter you can dry them in the oven on the absolute lowest warm setting, on an old towel, piece of newspaper or paper towel for 10 minutes or so. Something under it is a good idea in case when they cleaned them they left any wax or rosin on the tjap that might melt in the oven and drip down. Some folks blow them dry with a hair dryer too. The need to dry them quickly is so the steel handle and frame don't rust, or don't rust any more than it is already on the older ones.
When using them with batik wax mixtures, if you just want to use them and not display them or ever use them for anything else besides batik, simply let the wax cool and harden on them after use and store them in a plastic bag to protect them from dust so as not to contaminate your wax in future. Then just re-heat in your shallow wax pan to use again. If you want to re-use them for something else and need to remove the wax, there are several options. To get most of the wax off, you could heat them in an oven as above, with lots of absorbent paper towel under them. CAREFUL! a low heat is essential (~150-180°, depending on the type of wax), to melt the wax so it drips off, but not to generate bad fumes, or worse, toxic wax smoke, or make an oven fire! Obviously if you go this route, proper ventilation is essential. A safer way is to gently run HOT water over them, over a collection bucket or pan. You don't want that going down your sink. Solvents can be used, but more toxic and dangerous, so we don't recommend that route.
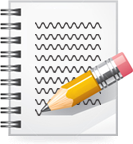