When mixing powdered Acid Dyes Dharma recommends the following dye dissolving procedure:
Always, always add liquid to powder, not powder to liquid.
Start with a cup of very hot (at least 180 degrees Fahrenheit) water and add about 1 tablespoon of that water to the powder. Smash the powder with a sturdy spoon while adding the liquid very gradually. This is called "pasting" the dye. We recommend this method for all colors. When it is a well-dissolved slurry, add the rest of the cup of water and stir vigorously. For hard to dissolve colors, try using hot Urea water (1-2 TBSP Urea/cup water) instead of plain water, or water at boil temp (212 degrees Fahrenheit) to paste up the dye. Also, let it sit for awhile, like half an hour, before you use it. With hard to dissolve colors that might be in a mix, this step can actually effect the final color you get.
To prevent freckling, strain your 1 cup solution into the dye bath water through something like thin pieces of silk (5 or 8mm Habotai works well) or fine nylon stockings placed in a funnel or strainer. If anything is left in the strainer paste it up with some more hot water and strain it again. Some colors in mixes dissolve much more slowly than the other color(s) and this solves that problem too. Experienced dyers will tell you it is worth this little bit of time to ensure a freckle free dye job! Also, because the raw colors, before U.S. manufacturers and distributors get hold of them and standardize them and make mixes with them, come from India and China usually, impurities like grains of sand or plastic particles are more common than they used to be years ago. Dharma makes sure all dye is sifted before packaging for this reason, but sifting doesn't catch everything. Straining the dye stock before using it is the next step. A great precautionary practice.
Urea is also especially helpful when making concentrated dye for painting or other direct application. One of its functions, besides being a humectant, is to allow more solids to go into solution in less liquid. Very handy in the dye world.
If you are using salt to help exhaust darker colors, add the pre-dissolved dye to the hot bath and mix well BEFORE adding salt. Salt reduces solubility, so if you do happen to have tiny particles of undissolved dye, they stand a better chance of going into solution without salt.
If you are making stock solutions with your dyes remember to re-heat them before you use them. It is normal for some acid dye colors, especially Acid Red 266, to fall out of solution when the water cools, or even to thicken and gel when very concentrated. Heating will restore them. Only mix as much concentrate as you can use in about a months time, after that the dyes will get weaker and give less vivid results.
Trouble shooting common problems/mistakes of newer Acid Dyers:
Freckling - see the above instruction on dissolving the dye, and straining for the more stubborn colors. Freckles, or small spots of color, are caused by clumps of undissolved dye striking in a small area on the fiber.
Splotchy or uneven Color , mixes separating - There are a few things that can cause splotchy results when dying solid colors. Even color is called Level. The term 'leveling' refers to the uniformity of the color. (Keep in mind that when you want deliberate color separation, mottling, etc., do the opposite of what is recommended to get level coloring!)
- Forgetting to Pre-wet the fabric - always soak your fabric in some cool to warm water with a couple drops of Kieralon before adding it to the dye bath. This will help the dye move through the fabric more evenly and help prevent areas from absorbing more dye then others. It will also help remove any fabric softener left on the material, which could inhibit dyeing.
- Not pre-washing - things like the above mentioned fabric softener, and even just oil from hands handling the silk or wool can cause splotchy dyeing, as well as silkworm gum, lanolin, machine oil, you name it. For level dyeing, fibers and fabric must be completely clean. Kieralon or Dharma Professional Textile Detergent and hot water work well for this.
- Over-crowding the goods - This is the most common factor in uneven dyeing. When fabric is bunched up, the dye pools in the folds and creates dark patches. Using a larger pot and more water will help reduce this problem. Bunching and dye pooling into the folds also happens when you don't stir enough.
- Heating the bath too fast - It is best to slowly raise the temperature of the dye bath once the dye and fabric have been added to slow the striking of the dye and give the dye molecules time to move through the fabric. Once the water is up to temperature THEN add the acid. Remember is takes heat and acid to make the dye fix, so the more gradually you increase them the more even your results will be.
- Uneven heat - It is important to frequently (but gently!) stir and flip your fabric/yarn/garment so that one section does not spend more time at the bottom of the pot than the rest. The bottom section of the pot is the hottest and dye will strike faster in the hotter areas of the pot.
- Adding the Vinegar (or citric acid) too early - Acid Dyes need heat and an acidic environment to strike and fix to the fabric. If you add the vinegar to the pot right before you add the fabric, the first end of the fabric ends up darker then the rest because as soon as the fabric hits the water dye starts to fix to it. Add your dye, stir it for a minute or two then add your fabric. Stir your fabric around in the dye for 5-10 min (longer for really large items) and let the dye evenly penetrate the material while you are getting the dye bath up to temperature. When you add the vinegar, push the material aside and add parts of it to different sides of the pot, or even pull the fabric out while adding the acid. Then stir the whole thing very thoroughly to make sure it is evenly mixed in as the dye often "strikes" very fast once the acid is added, and the less the fabric is moving, the more unevenly the dye will strike. This is especially important when using the pre-metallized dyes.
- The type of Acid Dye used to mix the color (or the type of Acid Dye in the purchased mix) - Milling and Premetallized dyes are very wash fast but sometimes they need a bit of help from a leveling agent. Commercial dyers use leveling agents to get the most even solid colors, such as adding Glauber's Salt to Leveling Acid Dyes (L) and using Ammonium Sulfate (used also for fertilizing plants and easy to find at gardening stores) instead of vinegar or citric acid with Milling (M) and Premetallized Acid Dyes (P). This allows the dye to attach itself to the fabric for a much longer time before the dye bath turns acidic and the dye "strikes". This is because Ammonium Sulfate stays a fairly neutral PH until the dye bath reaches about 150º F. This can also be duplicated by the suggestion above of adding acid to the dye bath much later in the process. Check out our article - "Did you Know how Acid Dyes Work" if you are a really serious wool/silk dyer and really want to get into the chemistry and types of Acid Dyes and how they work.
- Mixes of Acid Dyes with widely different chemistry or molecular weight, like mixing a Leveling Acid Dye with a Pre-metallized Acid Dye - the smaller molecules travel through the material faster than the big ones, which can cause colors to "separate" or "break". This separation is more common when using low immersion or direct application techniques, where it can be used to great advantage, but can be sometimes be seen in a dye bath situation as well.
- Low immersion techniques where steaming or microwaving is used to set the dye - in these situations where you don't have much water, the dye is trapped in the creases and folds. The fabric stays in one spot instead of swimming freely and moving when stirred in the bath situation. Different sized dye molecules, depending on the colors in the mix, migrate slowly through the fabric at different rates. It is perfectly normal to get color separation and blotchy results using these techniques. Artists use this to their advantage. Low immersion techniques are normally used to deliberately get color separation, as with tie-dye "bleed" that you see with fiber reactive dye on cotton. It is part of the beauty of low immersion dyeing or tie-dye techniques.
An unexpected color is coming up from a mixed color - usually seen at the beginning of a dye bath, but sometimes the end result too. More common with techniques that don't utilize the entire length and sequence of events as a "normal" dye bath, like baggie dyeing, microwaving, painting, steaming, etc. Also a great way to discover wonderful new effects of different mix combinations.
- Often when you have a mix of 2 or more colors, the pure colors in the mix are of a different molecular weight, size or composition, and some colors "strike" faster than others, even if the mix is of the same type of acid dyes. If you have a leveling dye (small molecules) mixed with a pre-metallized dye (much larger molecules), the leveling dye will strike much faster than the pre-metallized. The color you were expecting might not come up until very late in the dye bath. With mixes like this, it is very important to add your acid late in the process or use Ammonium Sulfate instead of Vinegar or Citric Acid.
- As mentioned above, a mix might have a hard to dissolve color in it, which dissolves later than other colors in the mix. Letting a color like this sit for ~30 minutes after you paste it up, then adding some more hot water before you use it, can help. We have found some of the blues are harder to dissolve, so the greens can come up yellower, and purples can strike more reddish than they should. Allowing more time for the blue to dissolve seems to solve this problem.
- Your end color is also affected by many other variables - water, fiber content, physical attributes of the fiber, etc. If you dye two different fiber types in the same dye bath, one may grab a color in the mix much faster than the other, hogging it, so the other fiber can come out a different color entirely. More absorbent fibers can come out a different color than less absorbent fibers, silk different than wool, etc. Put silk and wool in together, and the wool will absorb the dye much faster than the silk, and in different proportions of the mix components. Throw 5 different brands or types of wool yarn in the same dye bath of a mixed color and see what happens. Hard water can also yield different color than soft water. Technique alone can determine color; colors may come out differently depending on whether you do a full dyebath, microwave in a baggie, paint and steam, etc.
- If you have taken all these things into consideration, you can see if a color is possibly "off" by doing a "controlled" test, where you follow the dye bath directions to the letter with proper timing and proportions using a piece of common wool or silk and distilled water, or use water softener if you have "hard" water. You have to do it from start to finish, including the pre-washing and wetting, and through the washout and drying. That is the only way to ever tell if the problem is the dye, or one or more of the numerous other variables that effect final color.
The Dyes are not Exhausting - Sometimes the dye is not completely taken up by the fabric as is normal for Acid Dyes
- Too much dye - Double check your formula. We used 1.5% - 2% weight of goods (OWG) to get most of our colors of Dharma Acid Dye, except Black and Deep Navy (4%). Jacquard Acid Dyes have a chart in their instructions with specific amounts recommended for specific colors, ranging from 1.5% OWG all the way up to ~18% for the darkest colors. Remember - these % ratios are a starting point; you may need to increase or decrease the amount of dye depending on what you are dyeing and the environments, that you're working. At a certain point all the dye receptor sites on the fibers will be saturated. If you are happy with the color of the fiber pull it out and set it aside to rinse. Instead of tossing all the dye down the drain, stick some scrap fabric or yarn in and let it take up the rest of the dye. This is a great way to get new shades that may inspire a whole new project! Waste not want not. Also, some colors don't exhaust as well as others, but that does not mean you are not getting fixation.
- The color is not dark enough yet and the dye just doesn't seem to be striking or the dye bath is not exhausting - make sure you added your vinegar, even the best of us gets distracted by kids, pets, TV or a good sunny day. If you did add your vinegar but the water is still too dark and the fabric too light add some plain salt. One half to 1 full cup to start with; use more for dark colors like black and navy. Also, you can add more acid to cause more dye to strike.
- The water is almost clear but not quite - turn the heat off and let everything cool down. As the water cools its solubility decreases and this is often enough to encourage the last bit of dye to head into the fiber and fix. It is also good safety to let things cool before you pull out your item for rinsing.
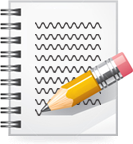